We offer
Grow your career
Jobs for seafarers
+35K people found jobs
Hot job vacancies for seamen
News and insights
Marine MANʼs News & Insights provides Ship Owner/Managers and Seafarers with marine expertise, guidance, surveys, and reports on todayʼs most relevant topics. What do we offer?
“Marine MAN” - Your Crew Manager
Omnes Viae Marine MAN Ducunt
Omnes Viae Marine MAN Ducunt
Marine MAN is pleased to serve as a one-stop-shop for the Ship Owners and Managers as strong and flexible Crewing Service Provider with a demonstrated history and deeply involved in the industry , combines advanced technologies with a personal touch.
We connect seafarers with Reputable Ship Owners and Managers ensuring optimal matches.We are proud to say that Marine MAN is Pioneer of Crewing Digital Innovation, created own crew recruitment soft and has completed long process of digitalization of all process, from recruitment to management and planning parts and become one of the 1st at the world full digital service provider.
We connect seafarers with Reputable Ship Owners and Managers ensuring optimal matches.We are proud to say that Marine MAN is Pioneer of Crewing Digital Innovation, created own crew recruitment soft and has completed long process of digitalization of all process, from recruitment to management and planning parts and become one of the 1st at the world full digital service provider.
Our areas of expertise
Crew management
Manning
Payment of wages to seafarers
Flag State Documentation for Seafarers
Recruitment Software
Technical management
S&P
Marine MAN — is an actively developing crewing company
Innovative methods in the company's policy make us a reliable partner for ship owners, as well as an excellent assistant for ratings and officers. Flexibility in decision-making, as well as integrity and responsibility, allows us to meet the requirements of the modern maritime industry.
What prospects do we open up for Ship Owners?
Ship Owners and Managers need reliable, professional crews, ready to work in difficult conditions. Marine MAN offers a full cycle of services for the selection and employment of seafarers, reducing the costs of shipowners for the search and selection of personnel.
By choosing us to select seafarers for work, you are guaranteed:
1. Flexibility of cooperation. We offer both one-time contracts and long-term crew supply programs.
2. Effective crew selection. Our database includes thousands of profiles of qualified seafarers of all ranks. We find talents taking into account the requirements of the shipowner.
3. Minimizing risks. Careful verification of documents, qualifications and experience of candidates allows to exclude mistakes during hiring.
Minimizing risks. Careful verification of documents, qualifications and experience of candidates allows to exclude mistakes during hiring.
By choosing us to select seafarers for work, you are guaranteed:
1. Flexibility of cooperation. We offer both one-time contracts and long-term crew supply programs.
2. Effective crew selection. Our database includes thousands of profiles of qualified seafarers of all ranks. We find talents taking into account the requirements of the shipowner.
3. Minimizing risks. Careful verification of documents, qualifications and experience of candidates allows to exclude mistakes during hiring.
Minimizing risks. Careful verification of documents, qualifications and experience of candidates allows to exclude mistakes during hiring.
Why is it easier to find a job in Shipping companies with us?
Every seafarer wants to work under decent conditions, receive a competitive salary and build a career. Of course, you can explore urgent vacancies for seamen on third-party resources or contact your friends to find interesting job offers. But sometimes such an independent search is not crowned with success, and also takes a huge amount of time.
Marine MAN — this is a real opportunity to find direct vacancies from Ship Owners, and, accordingly, stable work in the world's leading shipping companies.
What we offer to applicants:
1. Only verified vacancies. We work with reliable ship owners, excluding unscrupulous employers.
2. Convenient job search for seafarers. Our digital platform allows you to easily select vacancies in the maritime fleet by rank, experience, salary level and other criteria.
3. Possibility of connecting seafarers and ship owners. This is a great opportunity to communicate directly with future employers and clarify all the subtleties and details without intermediaries.
The main thing is that we help seafarers improve their skills, select more profitable seafarer’s employment contracts and build a long-term career in the maritime sector. With us, you will achieve completely different results than if you acted independently!
Marine MAN — this is a real opportunity to find direct vacancies from Ship Owners, and, accordingly, stable work in the world's leading shipping companies.
What we offer to applicants:
1. Only verified vacancies. We work with reliable ship owners, excluding unscrupulous employers.
2. Convenient job search for seafarers. Our digital platform allows you to easily select vacancies in the maritime fleet by rank, experience, salary level and other criteria.
3. Possibility of connecting seafarers and ship owners. This is a great opportunity to communicate directly with future employers and clarify all the subtleties and details without intermediaries.
The main thing is that we help seafarers improve their skills, select more profitable seafarer’s employment contracts and build a long-term career in the maritime sector. With us, you will achieve completely different results than if you acted independently!
Our Areas of Expertise
Marine MAN provides comprehensive solutions for shipping companies and seafarers. Our key areas of focus are:
1. Crew Management
As we have already said, we take care of all issues related to the recruitment and management of crews. Ship owners can be sure that the seafarers working on board their vessels are qualified and proven.
2. Maritime Payroll
Correct calculation of wages is the key to crew loyalty and efficient operation of the vessel. We will help ship owners determine the optimal wage level for seafarers, in accordance with international standards and requirements. Thanks to this, employment of seafarers will beeven faster and without problems.
3. Technical Management
Technical management. Monitoring the technical condition of vessels is another area of our work. We help ship owners maintain sea transport in good condition, organize repair work and monitor compliance with all regulatory requirements.
4. S&P
In addition to offering job vacancies for seafarers, we also have another line of business - we provide support in the purchase and sale of ships, helping ship owners find profitable offers and conduct transactions taking into account all legal and technical aspects.
5. Seafarer’s Flag State Documentation
Each ship flies the flag of a certain state, and seafarers need to complete the appropriate documentation. Marine MAN helps with obtaining, extending and completing all necessary documents in accordance with the requirements of the flag state.
We advise seafarers on certification, medical certificates and work visas to ensure their compliance with international standards.
But of course our main focus is offering vacancies for seafarers to work at sea.
We hire seafarers for:
1. Crew Management
As we have already said, we take care of all issues related to the recruitment and management of crews. Ship owners can be sure that the seafarers working on board their vessels are qualified and proven.
2. Maritime Payroll
Correct calculation of wages is the key to crew loyalty and efficient operation of the vessel. We will help ship owners determine the optimal wage level for seafarers, in accordance with international standards and requirements. Thanks to this, employment of seafarers will beeven faster and without problems.
3. Technical Management
Technical management. Monitoring the technical condition of vessels is another area of our work. We help ship owners maintain sea transport in good condition, organize repair work and monitor compliance with all regulatory requirements.
4. S&P
In addition to offering job vacancies for seafarers, we also have another line of business - we provide support in the purchase and sale of ships, helping ship owners find profitable offers and conduct transactions taking into account all legal and technical aspects.
5. Seafarer’s Flag State Documentation
Each ship flies the flag of a certain state, and seafarers need to complete the appropriate documentation. Marine MAN helps with obtaining, extending and completing all necessary documents in accordance with the requirements of the flag state.
We advise seafarers on certification, medical certificates and work visas to ensure their compliance with international standards.
But of course our main focus is offering vacancies for seafarers to work at sea.
We hire seafarers for:
Dry fleet
Wet fleet
Gas fleet
Passenger Fleet
Offshore Fleet
Regardless of your specialty and experience, we always have suitable vacancies on a ship. Marine MAN is not just a job search, it is an opportunity to confidently build a career in the maritime industry!
Marine MAN — reliability, proven over the years!
We know the maritime industry from the inside and understand how important it is for ship owners to have a qualified crew, and for seafarers to work with reliable employers. Our company combines many years of experience, modern technologies and a personal approach to each client.
By choosing us, you choose stability, professionalism and confidence in the future. Trust the experts who understand your profession better than anyone!
By choosing us, you choose stability, professionalism and confidence in the future. Trust the experts who understand your profession better than anyone!
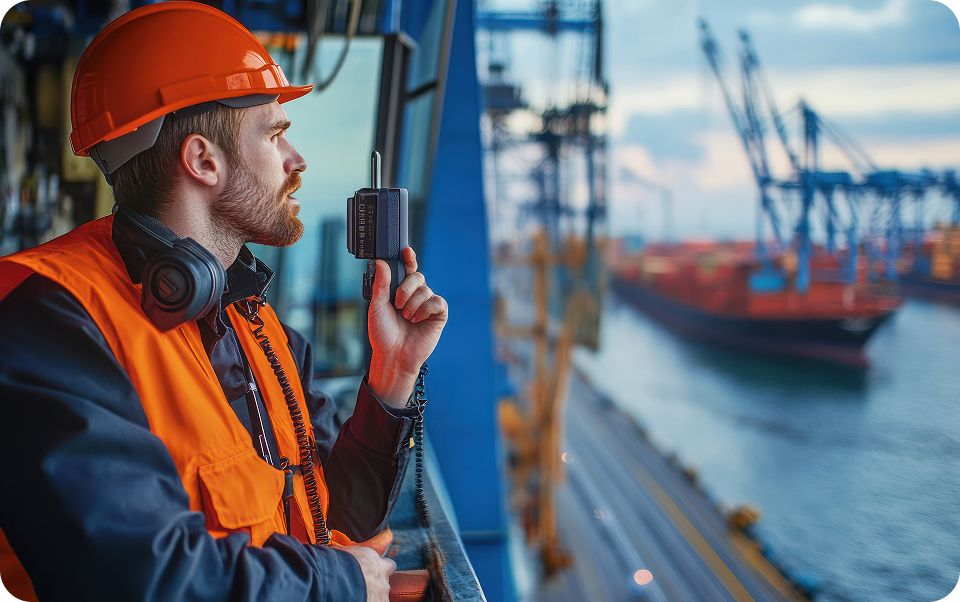
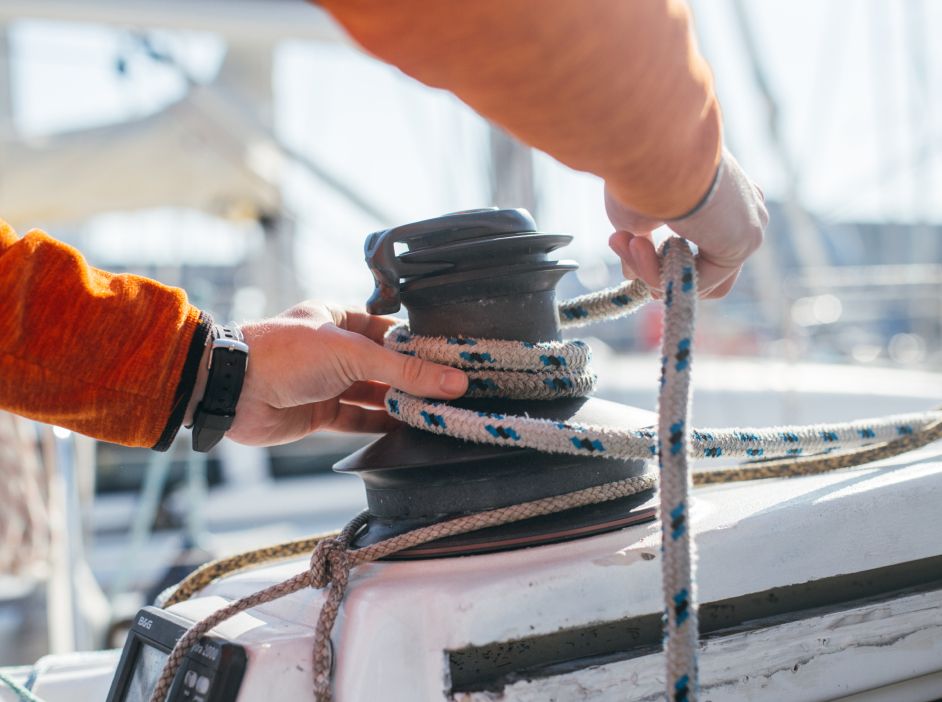